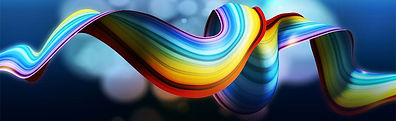
The ongoing development of inkjet technology and steadily growing printing volumes in companies and private households is continuously increasing requirements for aftermarket inks.
The demands on theaftermarket industry get more and more specific and complex, so technical expertise and practical experience areessential to the long term success of each recycler as well as for the industry as a whole. In the early days, cartridge technology was less complicated.
During that time, recyclers were able to fill any ink into existing tank cartridges without worrying whether the ink would come out of the print head.
Over the years, cartridge technology improved rapidly, and nowa-days the
technology can change from year to year, even from month to month.
Some factors that challenge ink manufacturers on a daily basis:
• Changed shape of cartridges
• Tank as well as foam cartridges
• Differing physical and chemical parameters of foams
• Filters above certain print heads
• Increased nozzle amounts
• Decreased drop size
• Dramatic acceleration of print speed
• OEM use of dye-based, black-pigment and color-pigment inks
It's no longer enough to know how to simply develop an ink. The functionality and technology of a cartridge has to be fully understood to develop an ink that will compete with the OEMs. This fact forces recyclers to keep pace and offer consumers a real alternative to OEM products. Therefore, the utmost modern state-of-the-art equipment is necessary when producing after-market inks, such as image analyzing systems,
particlesize measurement methods, Sun Testers, lR, UV-Vis, contact angle measurement devices, and various 3-Dmicroscopes that allow magnification of the print head interior. The three main factors necessary in the past for a recycler to produce a good quality product would havebeen easily summarized as follows:
1. Quality of empty cartridges
2. Quality of refilling equipment
3. Quality of ink
Nowadays the order of importance has turned upsidedown:
1. Quality of ink
2. Quality of refilling equipment
3. Quality of empty cartridge
Within the remanufacturing industry there are many filling methods practiced, such as hand filling, semi-au-tomatic filling, fully automatic filling and CISS systems. These methods, in conjunction with wet or dry foams, have led to an ability to fill to the OEM gross weight without having to compromise print quality and success rates. The right ink from manufacturers using pioneering technology and measurement parameters designed and developed to meet the exact requirements given by an OEM
ensures perfect performance and process properties across a wide production process spectrum.
Even fill quantities that exceed the OEM fill are possible with the right ink. This achievement adds value to the product and satisfies the consumer. Two of the most sensitive parameters for inkjet ink designs are surface tension and viscosity. They are the most important inseparable rheological properties of an ink.
Surface tension influences the wetting behaviour of the ink on the paper and inside the cartridge. lt affects edge sharpness, penetration of ink into print media, primary diffusion, optical density, color metric and color gamut, and ink flow inside a cartridge.
Viscosity is roughly defined as the thickness of substances (liquids, gases). lt defines and characterises the inner frictional resistance regarding flow processes (dynamic and kinematic viscosity).
Along with surface tension, viscosity influences the penetration of an ink into a print media, affects edge sharpness and controls the ink flow in a cartridge (foam) as well. Too high viscosity may block the ink flow completely and cause ink starvation. ln addition to changing technology,
the expectations and perceptions of the consumer when buying an alternative product have changed as well. In the past, the consumer was satisfied if the text printed black rather than grey and the print cartridge was reliable and saved money. Today, the average consumer is no longer happy with a simple standard print. The OEMs have conditioned consumers to expect better-performing printers and an improved output.
The Internet, digital cameras and mobile phones with cameras have created an environment where inkjet printers are nearly as common at home as TVs and coffee makers.
Consumers call on inkjet printers to complete tasks associated with work and print their photos at home. With this increased sophistication, consumers expect more from their print-outs, whether printed with OEM
or aftermarket products. When the consumer buys a printer, the first cartridge provided is an OEM, thereby setting the performance standard. The target of recyclers has to be persuading the consumer to buy a recycled product rather than an OEM cartridge. lf the consumer buys a recycled product that does not at least match the performance of the OEM product, even though it saves money and the environment, he will probably switch back to OEM. Thus, the philosophy of today's recyclers has to be competing with the performance of OEM products by using an ink that fulfills the requirements. Recyclers saving on ink costs may experience a short-term gain in a reduced cost pe rcartridge, but fail to meet ever-increasing expectations of consumers. This will result in a long-term loss for the recycler and for the whole industry. Competing only by price, not by quality, prevents the aftermarket inkjet industry from moving forward.
Filling a pigment cartridge with a dye-based ink in the past may have been enough to satisfy consumers, offices and home users, but today it is definitely not enough. Pigment inks out perform dye-based inks by far.
In offices, inkjet competes with laser, and only pigment inks can compete in optical densities and sharpness. However, not all pigment inks are created equal and merely choosing a pigment ink is not enough. Factors such as optical density, drying time, inter colour bleeding properties, highlighter resistance and print quality as a whole must be properly evaluated before choosing a formulation. Furthermore, it is not enough to
produce an ink that performs well today but does not maintain its characteristics tomorrow. The stability of the used dispersion is a key factor for the long-term stability of the ink. Most pigment dispersions available on the market consist of polymers and surfactants to stabilise them. These attached molecules keep the pigments pending in the dispersion, for stabilisation, but the polymers effectively bind the pigments and have the tendency to dry and adhere to the cartridge when first refilled. Pigment inks in which pigments are electrostatically charged are stabilised by molecule groups chemically and permanently bonded to the pigment surface; therefore they do not have the drying problems of polymeric dispersed pigment based inks.
The charged stabilising groups attached to the pigment surface also function as binders upon drying, but only when making contact with paper. The groups attached to the pigment surface, when not in contact with paper, combine well with water and other components of the ink vehicle. In the print head, even if drying occurs, these types of inks are easily able to be redispersed. lt is similar to a dye ink that uses the above described electrostatic stabilisation technology, except with the ability to achieve significant improvements in print performance properties such as line clarity, opti-cal density, inter color bleeding properties, water fastness and light fastness. This short insight to the challenges of an ink manufacturer helps us see how both recyclers and ink manufacturers can work together to help the industry move forward and increase market share of alternative inkjet cartridges by providing a product that competes in quality with OEM product.
Keeping Ink Quality Constant
In an Ever-Changing Ink-Jet Market...
